在化工、制药、粮食加工等存在爆炸性环境的工业场景中,螺旋上料机和螺旋提升机作为核心输送设备,其安全性能直接关系到生产安全。本文从防爆风险、防爆认证改造和防静电措施三方面展开分析,为相关行业提供技术参考。
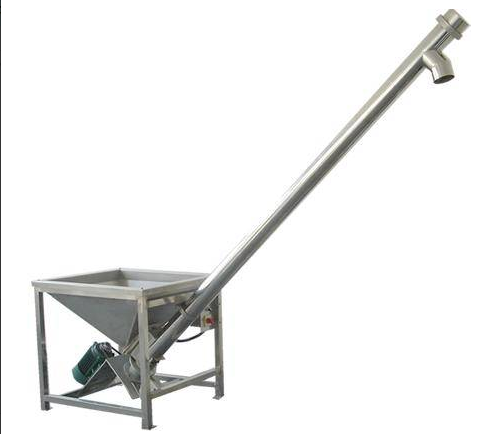
一、防爆区域使用螺旋设备的主要风险
粉尘爆炸风险
在粮食加工、化工等领域,物料输送过程中产生的粉尘(如淀粉、金属粉末等)易形成爆炸性混合物。螺旋上料机的叶片与物料摩擦可能产生静电或火花,若设备未采取防爆设计,极易引燃粉尘云。例如,某案例中因设备未采用非金属畚斗,金属摩擦导致粉尘爆燃,造成严重事故。气体爆炸风险
在石油、天然气或溶剂处理场景中,挥发性气体可能泄漏至设备内部。若螺旋提升机的电机或轴承未达到防爆等级,运行时的电火花或高温表面可能成为点火源。某化工厂曾因普通电机在氢气环境中运行引发爆炸,直接经济损失超千万元。机械故障隐患
设备部件(如轴承)润滑不足或磨损可能导致局部过热,甚至引发金属碰撞火花。例如,某化工厂因螺旋上料机的轴承故障导致氢气泄漏爆炸,事故调查显示设备缺乏定期维护是主因。
二、防爆认证改造的关键要点
设备分类与区域适配
针对爆炸性环境,需根据实际工况对设备进行分类适配:
气体与粉尘环境区分:螺旋提升机在粉尘环境中需确保表面温度控制,避免热量积聚引发自燃。
防护等级匹配:在氢气等高危气体环境中,设备需采用密闭结构并配备惰性气体保护系统。
防爆电机与结构优化
电机选型:采用防火外壳或增强安全型电机,确保内部爆炸不扩散至外部。例如,某品牌防爆电机通过特殊设计,将运行温度控制在安全阈值内。
材质升级:化工行业常用不锈钢材质螺旋上料机,并采用全密封设计防止粉尘或气体渗入。
改造流程与测试验证
防爆认证改造需完成以下核心步骤:
风险评估与方案设计:根据爆炸性环境特性制定改造方案,例如在氢气环境中增加氮气吹扫装置。
样机测试与性能验证:通过模拟工况测试设备的防爆性能,包括高温、火花防护等关键指标。
追溯标识与文档管理:改造后设备需标注防爆等级、温度限制等信息,并留存完整的改造记录。
三、防静电措施的实施
材料与接地优化
导电材料应用:在粉尘环境中,螺旋提升机的输送带可采用碳纤维复合材料,并通过多点接地导出静电。
非金属部件设计:使用抗静电塑料制作叶片,减少摩擦电荷积累,例如某食品厂改造后静电电位降低80%。
运行环境控制
湿度管理:保持环境湿度≥60%,抑制静电产生,尤其适用于粮食加工场景。
惰性气体保护:向设备内部注入氮气,降低氧气浓度至爆炸极限以下。
维护与监测技术
清洁与润滑规范:定期清理螺旋上料机的轴承和驱动部件,避免粉尘堆积引发摩擦起火。
实时监控系统:安装静电传感器和温度探测器,实现异常状态的自动报警与停机。
四、应用案例与行业实践
某跨国化工企业将传统螺旋提升机改造为防爆版本,主要措施包括:
更换防爆电机,适配氢气高危环境;
加装抗静电涂层与多点接地装置,静电风险显著降低;
执行定期维护计划,设备故障率下降70%。
结论
螺旋上料机和螺旋提升机在防爆区域的安全运行,需综合防爆认证改造、防静电设计与严格运维管理。随着行业技术的进步,设备制造商应优先采用模块化防爆设计,并通过权威机构认证,以满足爆炸性环境的复杂需求。在化工、能源等高危领域,技术创新与规范执行是保障螺旋设备安全的核心基础